Unlike regular cleaning, which often involves surface-level tasks, an industrial deep clean dives much deeper, ensuring every nook and cranny of a facility is spotless and sanitized.
This article delves into the major aspects involved in a deep clean for industrial facilities.
Industrial Machinery
CNC machines, vital for precision tasks, can experience issues with their spindle due to the accumulation of dust, metal shavings, and lubricants. This buildup affects the spindle’s rotation and precision. Similarly, the coolant systems in these machines can get clogged by residue and contaminants, leading to inefficient cooling and potential overheating.
The guideways and slides of CNC machines are not immune either; dirt and debris can introduce friction, causing wear and imprecise movements.
Conveyor systems, often used to transport materials and products, face their own set of challenges. The belts can collect spills, dust, and debris, which might result in slippage and misalignment. The rollers in these systems are susceptible to material buildup that can hinder their smooth rotation, leading to jams. Additionally, the drive gears in conveyor systems can malfunction due to the interference of dirt and grime with the meshing of gears.
Hydraulic presses, pivotal in many manufacturing processes, rely heavily on their cylinders and valves. Contaminants in the cylinders can lead to seal damage, causing inefficiencies due to leaks.
Similarly, dirt and debris can make valves sticky or prevent them from sealing properly, affecting the overall operation of the machine.
In the realm of plastic manufacturing, injection molding machines can suffer from performance degradation due to residual plastic and contaminants in their screw and barrel. The clamping unit, responsible for holding molds securely, can also be affected by dirt, leading to defects in the final product.
Mixing and blending equipment, essential for combining materials, can see a decline in their performance when blades and paddles have residue buildup. This affects their ability to mix materials thoroughly.
Seals and gaskets in these machines are not exempt; contaminants can induce leaks, leading to both product contamination and loss.
Lastly, in the packaging sector, machinery faces unique challenges. Sealing components in packaging machinery can be rendered ineffective due to dust and debris, potentially leading to product spoilage. The feed systems, responsible for the smooth flow of products, can experience jams if residue accumulates, slowing down the entire packaging process.
Industrial Floor and Surface Sanitation Services
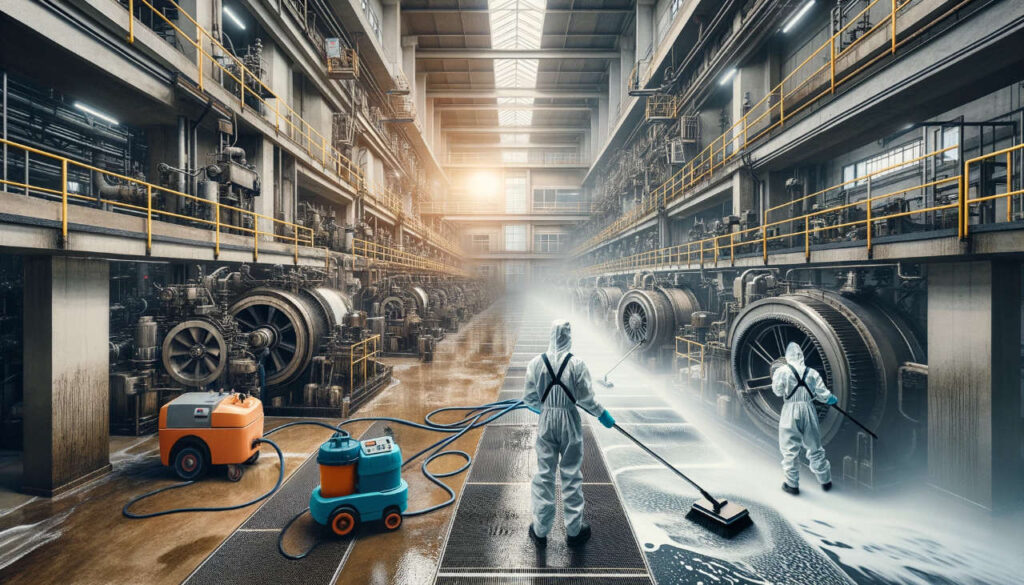
Floors are subjected to heavy foot traffic, inadvertent spills, and the constant grind of machinery. Over time, these floors can become stained and accumulate layers of grime and dirt. But it’s not just about the visible marks or dirt; the real concern often lies in the unseen.
Bacteria, fungi, and various pathogens can thrive on these surfaces, posing a significant health risk to employees and potentially contaminating products.
To mitigate this, specialized cleaning solutions are employed. These are not just designed to tackle tough stains and dirt but also have the capability to eliminate microorganisms, ensuring a sanitized surface.
The process often combines mechanical scrubbing with chemical treatments to ensure a thorough cleanse. The result is not just a clean-looking floor but one that’s truly hygienic, free from potential health hazards.
Beyond the floors, other surfaces in industrial facilities, such as worktables, walls, and storage units, also demand attention. These surfaces, while perhaps not as exposed as floors, can still harbor contaminants.
Overhead structures, for instance, can collect dust and, over time, release it onto the products or machinery below. Worktables, where parts are assembled or products are packed, can gather residues from materials, which can lead to cross-contamination if not addressed.
Air Ducts & Ventilation System Cleaning
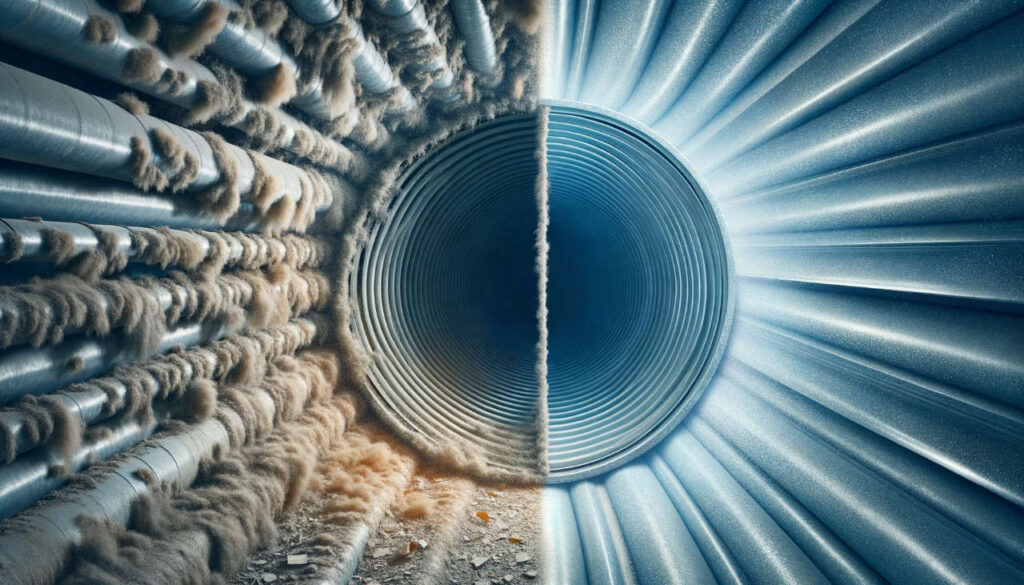
Over time, air ducts and ventilation systems can become a hotspot for various pollutants. Dust, mold spores, and other airborne contaminants can accumulate within these systems. As the air circulates, these pollutants can be distributed throughout the facility, potentially degrading air quality and posing health risks to employees. For machinery, poor air quality can lead to inefficiencies, as some equipment relies on clean air for cooling and operation.
For instance, consider the extraction systems often found in manufacturing plants dealing with volatile chemicals or fumes. These systems are designed to remove harmful vapors from the workspace. However, when the ducts of these systems become clogged or lined with residues, their efficiency can diminish, leading to a build-up of harmful substances in the air.
Similarly, in facilities where temperature control is vital, such as in food processing plants, compromised ventilation can lead to uneven cooling or heating. This not only affects the quality of the products but also the machinery’s operational efficiency.
The cleaning process for these ventilation systems is meticulous. It often involves specialized equipment that can navigate the twists and turns of ductwork, combined with cleaning agents that can break down and remove stubborn residues. Moreover, filters within these systems are either cleaned or replaced to ensure optimal air filtration.