Keeping industrial HVAC systems clean protects airflow, air quality, and equipment performance across every corner of your operation.
Below is a checklist of HVAC and air cleanliness tips specifically for industrial spaces. Each one highlights tasks that often fall between the cracks — many of which can be handled by a qualified cleaning partner as part of regular facility upkeep.
Clean HVAC Coils and Drain Pans Quarterly
Even well-maintained systems can suffer when coil surfaces and drain pans are ignored. Over time, dust, grease, and microbial growth build up in these components (especially in high-output environments like manufacturing or logistics). This reduces system efficiency and introduces musty odors or airborne bacteria into your facility.
Cleaning coils and drain pans involves removing access panels, applying a non-corrosive coil cleaner, and flushing buildup with water or steam. This includes vacuuming or wiping down pans to prevent clogs and standing water.
For a mid-sized rooftop or interior unit, the process can take 1–2 hours per system, depending on accessibility.
While HVAC techs may check these during seasonal maintenance, cleaning them thoroughly often falls outside their scope. A qualified cleaning crew can include coil cleaning in quarterly deep cleans, especially in zones where production contaminants are heavy.
Seal Gaps Around Ductwork and Access Panels
Unsealed ductwork is both an efficiency and air quality issue. Any gaps, cracks, or poorly sealed access panels in your system can pull in contaminated air from attics, utility spaces, or maintenance corridors. That means dust, insulation fibers, or even fumes from adjacent areas can bypass your filters entirely and circulate through your facility.
Locating and sealing these leaks usually involves a visual inspection of duct seams, joints, and access panels, followed by applying UL-rated foil tape or mastic sealant. In larger facilities, this process may be broken into zones and tackled over time — but sealing one rooftop unit and its accessible ductwork typically takes 1–2 hours.
Because these small leaks aren’t always obvious unless airflow is being tested, they often go unnoticed. A proactive cleaning partner can help identify and report problem areas during routine overhead dusting or vent servicing — so your HVAC contractor can fix them before they impact performance.
Degrease Vent Covers and Returns — Not Just Filters
Filters catch airborne particles, but if your vent covers and return grilles are coated in dust or greasy residue, you’re still pushing dirty air through the system. This is especially common in facilities with heavy equipment, forklifts, or nearby production areas where vapors and oils are present.
Over time, that buildup restricts airflow and can even drip onto floors or workspaces.
Degreasing involves removing vent covers (when possible), soaking or wiping them down with a degreasing agent, and drying thoroughly before reinstallation. In zones with overhead returns or hard-to-reach ceiling vents, this may require ladders, lifts, or extension tools.
Cleaning a set of 4–6 vents in a production zone typically takes 30–60 minutes, depending on buildup and access.
Establish a Zone-Based Cleaning Rotation for Ceiling Vents
Ceiling vents are some of the most overlooked components in industrial air quality. Out of sight, out of mind — until you notice black streaks on the ceiling tiles or dust flakes falling into workspaces. Left unchecked, these vents quietly recirculate built-up grime back into the air, undermining filtration efforts and creating a poor impression on visitors or inspectors.
Rather than trying to tackle every vent at once, break your facility into cleaning zones (e.g., production floor, packaging area, admin offices) and rotate through them monthly or quarterly. Cleaning typically involves vacuuming or brushing the vent face, wiping it down with a microfiber cloth and appropriate cleaner, and checking for visible buildup inside the duct throat. For moderately dusty vents, a team can clean 8–12 ceiling vents per hour depending on ceiling height and access.
This kind of proactive rotation ensures no area gets too far behind — and it helps you stay ahead of both air quality complaints and cosmetic issues. A trained cleaning crew can track and manage these rotations in tandem with your existing cleaning schedule, so it’s one less thing for your team to chase down.
Monitor Negative Pressure Near Exhaust Fans and Doorways
Pressure imbalances can quietly sabotage your indoor air quality. When certain areas of your facility operate under negative pressure — typically caused by strong exhaust fans or poorly balanced ventilation systems — they can draw in unfiltered air through door gaps, loading docks, or wall penetrations. That air may carry dust, pollen, exhaust fumes, or humidity, especially near open bay doors or exterior entries.
Detecting this issue doesn’t always require expensive testing equipment. A simple smoke pencil, tissue strip, or even incense stick can help identify areas where air is being pulled inward. Once identified, resolving the imbalance often means adjusting ventilation airflow, adding makeup air supply, or in some cases, sealing unplanned openings. The check itself takes just a few minutes per doorway or fan zone — and can be built into a regular walk-through.
Cleaners may not be responsible for the airflow mechanics, but they’re often the first to notice the signs: accelerated dust buildup near doors, damp thresholds, or complaints about odors near specific entryways. Flagging these early can help facility teams make ventilation corrections before IAQ or comfort suffers.
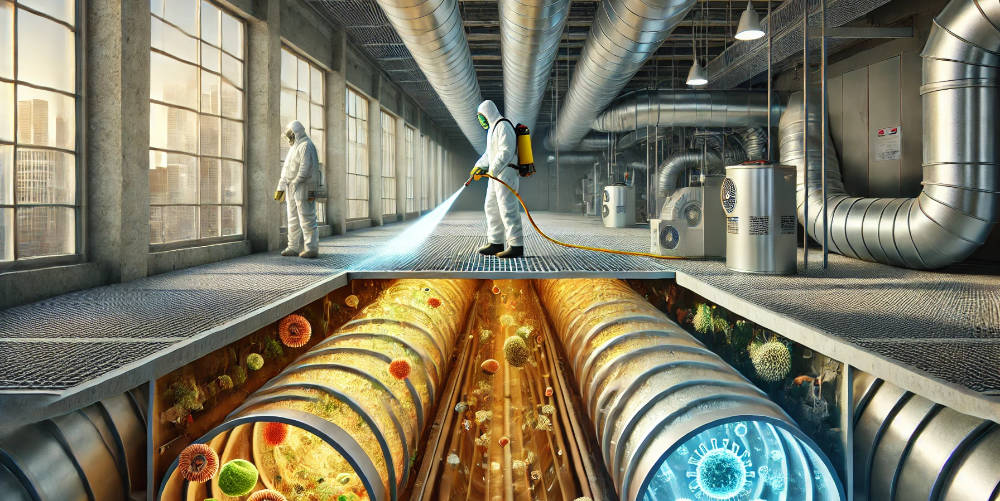
Use Antimicrobial Treatments in Air Ducts — with Caution
In sensitive environments like food processing, pharmaceuticals, or healthcare-adjacent manufacturing, microbial control in air systems isn’t just a “nice to have” — it’s a compliance necessity. But even in general industrial spaces, mold, bacteria, and biofilm can accumulate inside ductwork and HVAC components over time, especially in humid conditions or where condensation forms.
The maintenance process usually involves:
- Temporarily shutting down the system
- Applying a registered antimicrobial agent via ULV fogger or sprayer
- Allowing appropriate dwell time
- Restarting the system once dry and safe
Antimicrobial duct treatments help suppress mold, bacteria, and biofilm in hard-to-reach internal surfaces. This is especially valuable:
- In food processing areas, where airborne contamination could impact exposed product zones or violate USDA sanitation standards.
- In medical or pharmaceutical facilities, where airborne microbes can compromise sterile environments or contaminate packaging lines.
- In humid or high-condensation zones, where standing water in drain pans or duct low points can become breeding grounds for mold.
The treatment process involves shutting down the system, applying a registered antimicrobial fog or spray via ULV foggers, allowing appropriate dwell time, and ventilating before restarting. The entire process for a zone or air handling unit typically takes 1–2 hours and is often done after hours to avoid exposure.
Importantly, not all antimicrobial products are safe for HVAC materials or indoor use — so facility managers must choose EPA-registered products rated for HVAC systems. While this work is usually performed by HVAC or IAQ contractors, a professional cleaning crew can prep the area, clean vent access points, and monitor for signs of future microbial buildup as part of ongoing maintenance.
Schedule Off-Hour Deep Cleaning of Air Intakes and Rooftop Units
Rooftop HVAC units and exterior air intakes are your facility’s first line of defense against outdoor contaminants — but they’re often neglected simply because they’re out of sight. Leaves, pollen, bird droppings, industrial dust, and even trash can collect around intake vents and inside rooftop housings, leading to reduced airflow, foul odors, and premature filter clogging.
A deep clean typically includes:
- Clearing debris from around the intake or unit
- Vacuuming and wiping down intake screens and louvers
- Cleaning the surrounding roof surface to prevent recontamination
- Checking for signs of nesting, corrosion, or blockage
Depending on unit size and access requirements, a rooftop HVAC cleaning takes 1–2 hours per unit. If intake screens are heavily clogged or bird deterrents are in place, additional time may be needed. It’s best to schedule this outside of production hours, since exterior intakes may be temporarily blocked or opened during cleaning.
While HVAC technicians inspect these units seasonally, they rarely perform detailed cleanings unless requested. A cleaning partner familiar with rooftop safety can integrate this into a quarterly or semi-annual service, helping you prevent costly performance issues caused by outdoor debris before they ever enter your system.
Replace or Wash Pre-Filters — Not Just Final Filters
Final filters get all the attention, but it’s your pre-filters that quietly determine how long those final filters actually last. Pre-filters are the first line of defense, capturing larger particles like dust, fibers, and debris before air hits the more expensive high-efficiency filters deeper in your system. If pre-filters are clogged — or worse, missing — your final filters can become overloaded and fail prematurely.
In most industrial facilities, pre-filters should be inspected monthly and replaced or cleaned every 1–3 months depending on your environment. In dusty zones (like woodworking, metal grinding, or loading docks), more frequent changes may be needed. Replacement typically takes 15–30 minutes per unit, depending on how many pre-filter slots there are and how accessible they are.
Since pre-filters are often cheaper and easier to handle, it’s tempting to let them ride — but doing so shortens the life of your more costly final filters and compromises airflow throughout the system. A smart cleaning rotation can include visual inspections and reporting on pre-filter condition so facility managers know when to bring in HVAC support for replacement.
By integrating the tips above into your regular maintenance routines, you not only extend the life of your HVAC system — you create a cleaner, safer environment for everyone in the building.
If you’re in the Greensboro, Winston-Salem, High Point, or Burlington area and want a cleaning partner who thinks beyond floor shine and garbage bags, we’d be happy to talk. Carolina Services of the Triad works side-by-side with facility teams to keep critical systems clean, compliant, and performing at their best.