Industrial cleaning is a vital component of many sectors, ensuring the upkeep of hygiene standards, worker safety, and efficient operations. However, this industry is not without its challenges, demanding a high level of adaptability, expertise, and innovative problem-solving strategies.
The companies at the forefront of this industry tackle these hurdles by developing customized solutions to meet the distinct needs of their clients and staying abreast of evolving regulations and new technologies.
The right cleaning company can navigate these challenges, providing innovative and effective solutions to maintain optimal hygiene standards.
Challenge 1: Adhering to Diverse Regulations
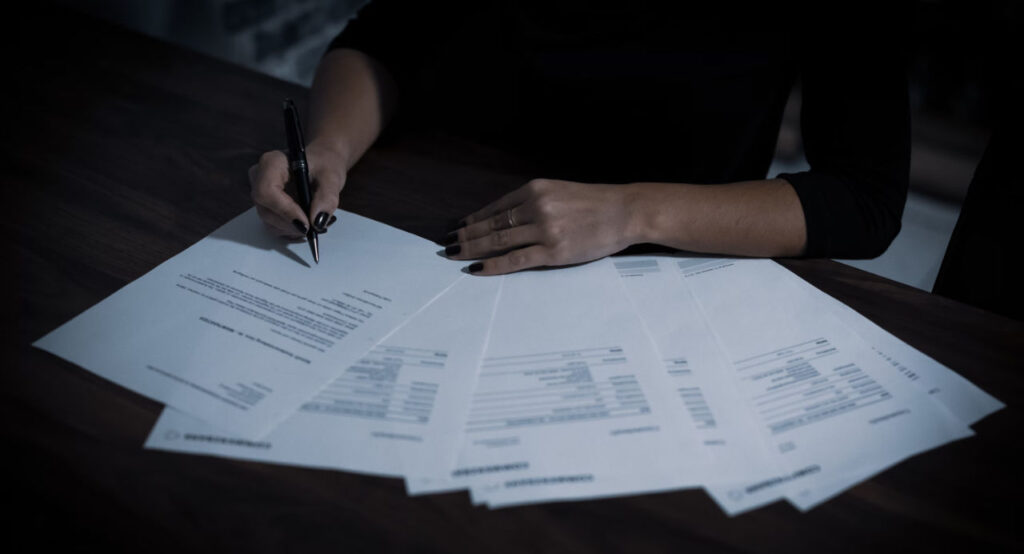
Every industry operates under a unique set of rules and standards established by regulatory bodies to ensure safety, quality, and ethical practices.
When it comes to cleaning, these rules often focus on sanitation, hygiene, and waste disposal to prevent contamination and maintain a safe working environment.
For instance, a food processing plant will need to follow the strict sanitation guidelines set by the Food and Drug Administration (FDA) and the United States Department of Agriculture (USDA). These rules often include the use of food-safe cleaning agents, regular deep cleaning of equipment, and proper disposal of waste to prevent cross-contamination.
In contrast, a pharmaceutical company would need to adhere to Good Manufacturing Practice (GMP) guidelines, which focus on maintaining product integrity to ensure patient safety.
These guidelines might include regular cleaning and sterilization of production equipment, the use of specific cleaning agents that won’t leave residue, and meticulous documentation of all cleaning procedures.
Meeting these diverse requirements is a significant challenge for any industrial cleaning company. One size certainly does not fit all, and a cleaning approach that works for one client might be completely inappropriate for another.
Solution: Customized Compliance Frameworks
To achieve this, a savvy cleaning company would create a dedicated compliance team responsible for staying up-to-date with all relevant industry regulations. This team would work closely with the client to understand their specific needs, develop a tailored cleaning protocol, and ensure that the cleaning staff are adequately trained to follow it.
For example, in an industry where allergen cross-contamination is a risk, like in a food processing plant that handles both peanuts and non-nut products, the cleaning company might develop a rigorous allergen management plan.
This could include segregating cleaning equipment to prevent cross-contact, implementing specific cleaning procedures to eliminate allergens, and conducting regular audits to ensure compliance.
Challenge 2: Dealing with Hazardous Materials
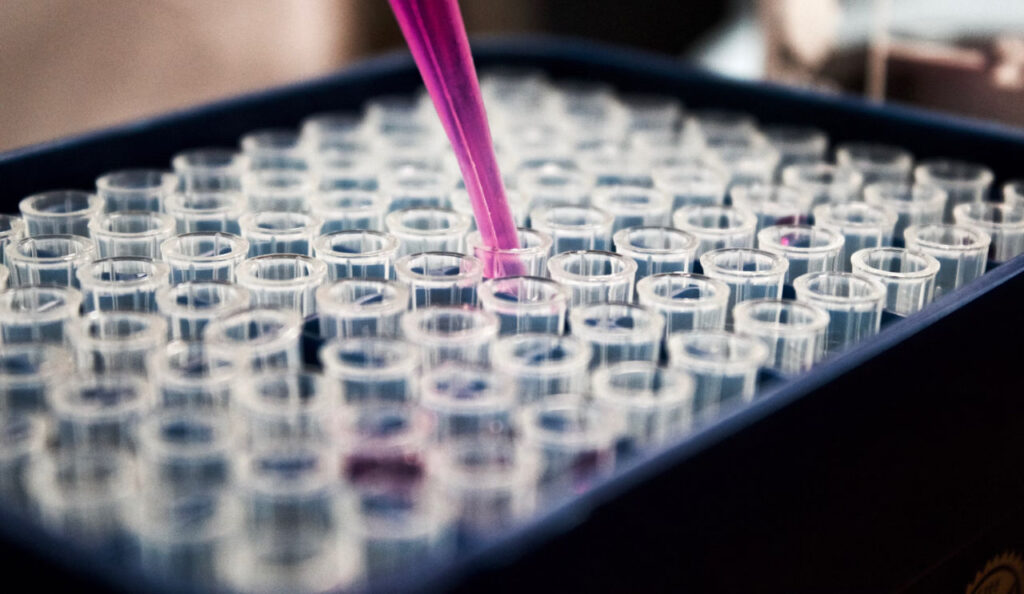
Industrial facilities quite often handle hazardous substances, such as toxic chemicals, volatile organic compounds (VOCs), biological waste, or radioactive materials. These substances pose significant risks to the health and safety of cleaning personnel, as well as to the environment if not properly managed.
Improper handling or disposal can also lead to hefty fines and legal penalties due to environmental regulations.
For example, in a chemical manufacturing plant, cleaning personnel might encounter residues of dangerous substances such as acids or solvents. Prolonged or improper exposure to these substances can lead to severe health problems, from skin burns and respiratory issues to more serious long-term conditions.
In a healthcare facility, cleaning staff might have to deal with biological hazards like blood-borne pathogens, which can potentially transmit diseases. There’s also the risk of exposure to radiation in facilities that use radioactive materials, such as certain types of research labs or medical testing facilities.
The solution to this challenge comes in two parts.
Advanced Training
The cleaning company should provide comprehensive training to its personnel to ensure they understand the risks associated with different types of hazardous materials and how to handle them safely. This includes the proper use of personal protective equipment (PPE) such as gloves, masks, and protective suits, as well as safe procedures for handling and disposing of hazardous waste.
For instance, in a healthcare setting, this could involve training on standard precautions to prevent the spread of infection, such as using disposable gloves and gowns, safely disposing of sharps (like needles), and correctly sterilizing reusable equipment.
These are things our cleaning company takes very seriously, and we’ve had good relationships with medical facilities with clean rooms as well as manufacturing plants over the years.
Green Cleaning
In addition to safe handling practices, the company can also implement green cleaning strategies to reduce the use of hazardous cleaning products and promote environmental sustainability.
Green cleaning involves the use of cleaning agents that are biodegradable, low in toxicity, and free from environmentally harmful ingredients. It can also include practices such as reducing water usage and recycling cleaning equipment.
For example, the company might use microfiber cloths and mops, which are not only more effective at capturing dust and dirt, but also require less water and fewer chemicals to do the job. Or they could employ steam cleaning or UV-C light sterilization, which can effectively kill bacteria and viruses without the use of harsh chemicals.
By combining advanced training with green cleaning practices, an industrial cleaning company can effectively mitigate the risks associated with hazardous materials, ensuring the safety of their workers, their clients, and the environment.
Challenge 3: Keeping HVAC Systems From Causing Safety Issues
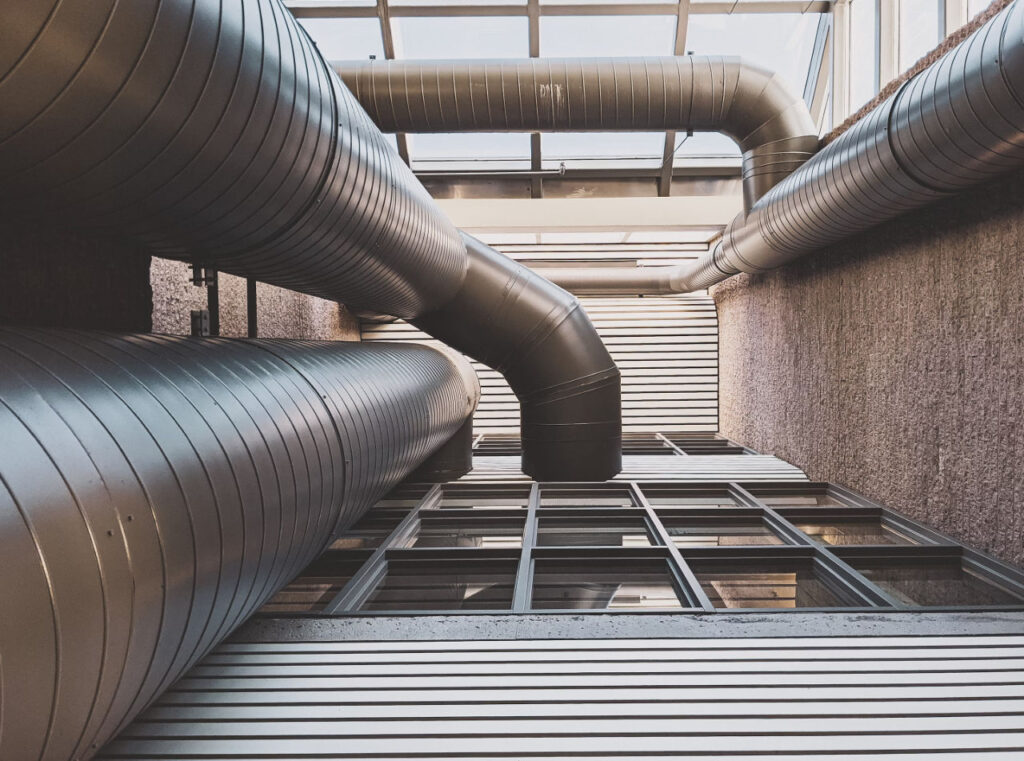
These systems are responsible for ventilating fumes and controlling the indoor air quality, which, if not correctly managed, can result in exposure risks for workers and potential regulatory non-compliance.
certain substances can cause rapid deterioration of metal ductwork or coils, leading to leaks and reduced system efficiency. Such degradation can result in harmful chemicals leaking into the ventilation system and potentially circulating throughout the facility, posing significant health risks.
Another concern is the accumulation of chemical residues within the system. Over time, these residues can build up, reducing system efficiency and leading to a decline in indoor air quality.
The Solution for HVAC Maintenance:
Routine inspections involve thorough checking of the HVAC system, including ductwork, coils, filters, and air handling units.
During these inspections, the team looks for any visible signs of corrosion or wear, checks system performance indicators such as airflow and temperature, and tests for any potentially hazardous chemical residues in the air or on the system components.
Take a manufacturing plant dealing with corrosive substances, for example. Routine inspections can prevent a minor leak in the ductwork from escalating into a major problem.
Spotting the issue early allows for timely repairs, preventing the corrosive substance from causing extensive damage to the HVAC system or contaminating the air breathed by the plant’s employees.
The role of specialized cleaning procedures is also paramount. Teams trained in handling hazardous materials use specific cleaning agents and methods to effectively remove chemical residues without causing harm to themselves or the system components.
For instance, in a chemical lab dealing with heavy metal compounds, specialized cleaners could use high-efficiency particulate air (HEPA) vacuum cleaners to safely remove any residual metal dust from HVAC components, reducing the risk of harmful particles being recirculated into the air.
Routine inspections involve thorough checking of the HVAC system, including ductwork, coils, filters, and air handling units. During these inspections, the team looks for any visible signs of corrosion or wear, checks system performance indicators such as airflow and temperature, and tests for any potentially hazardous chemical residues in the air or on the system components.
Take a manufacturing plant dealing with corrosive substances, for example. Routine inspections can prevent a minor leak in the ductwork from escalating into a major problem. Spotting the issue early allows for timely repairs, preventing the corrosive substance from causing extensive damage to the HVAC system or contaminating the air breathed by the plant’s employees.
The role of specialized cleaning procedures is also paramount in medical facilities. Teams trained in handling hazardous materials use specific cleaning agents and methods to effectively remove chemical residues without causing harm to themselves or the system components.
For instance, in a chemical lab dealing with heavy metal compounds, specialized cleaners could use high-efficiency particulate air (HEPA) vacuum cleaners to safely remove any residual metal dust from HVAC components, reducing the risk of harmful particles being recirculated into the air.
High-grade cleaning and sterilization agents are used to kill any bacteria, viruses, or fungi present. For example, in a hospital setting, UV-C light sterilization could be used in the air handling units to kill any airborne pathogens before they are circulated throughout the building.
Strict control of environmental conditions involves careful monitoring and adjusting of temperature, humidity, and pressure differentials. These factors are critical in preventing the spread of pathogens.
For instance, in an intensive care unit (ICU), maintaining the right humidity levels can help inhibit the growth of bacteria and viruses. Similarly, maintaining positive pressure in an operating room prevents airborne pathogens from other parts of the hospital from entering the sterile environment.
Finally, rigorous adherence to safety standards ensures that all practices are in line with health regulations. Regular audits and inspections are conducted to ensure all system components are functioning correctly and all safety protocols are being followed.
For instance, in isolation wards for highly contagious diseases, safety checks might include testing the seal of the room to ensure no air is escaping, verifying the proper functioning of HEPA filters, and checking UVGI systems for correct operation.